Przypadki użycia
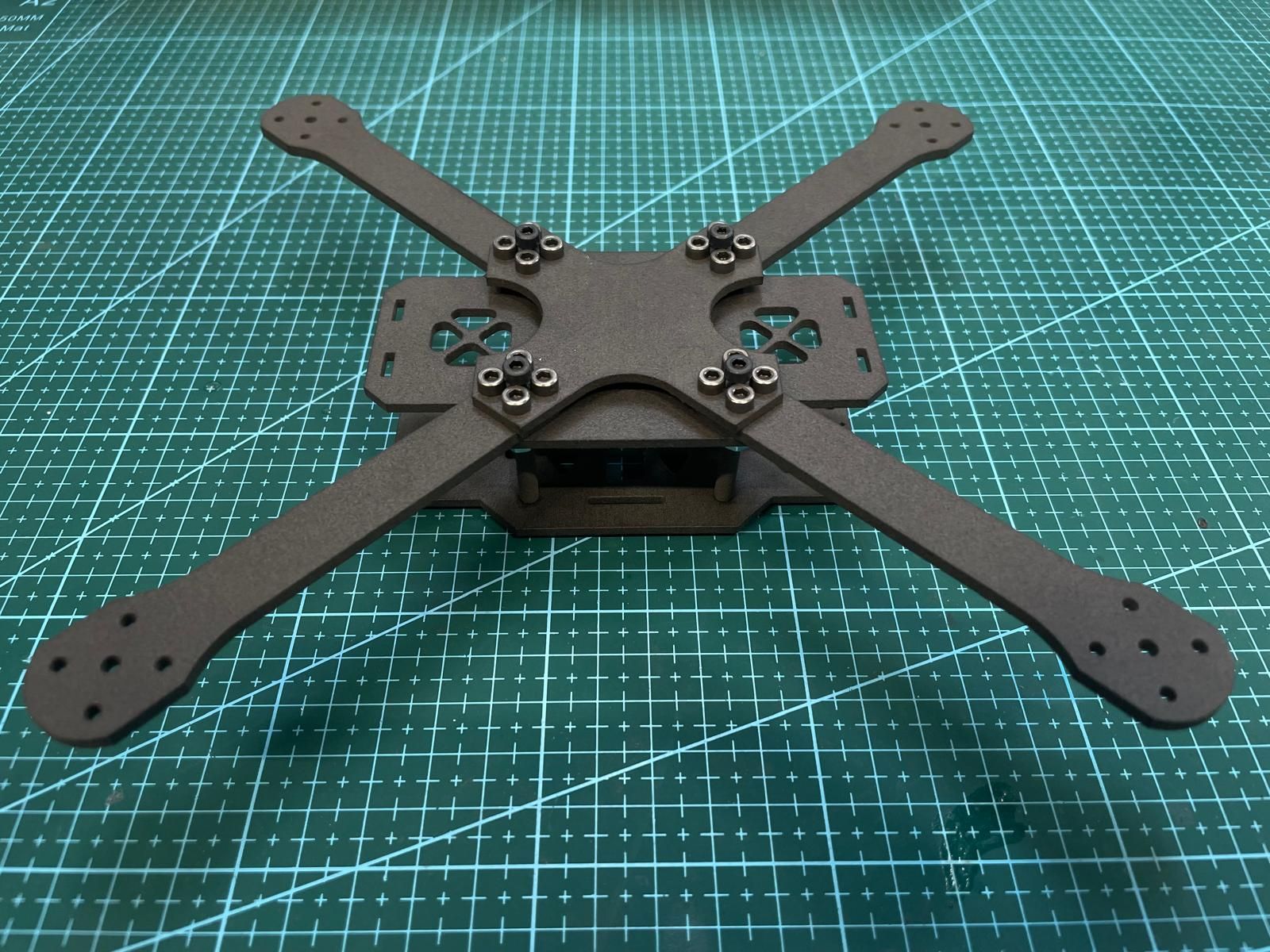
Prototypy i personalizacja produktów Personalizacja produktów staje się dziś jednym z kluczowych trendów w przemyśle i usługach. Odpowiadając na rosnące oczekiwania klientów, Hydropress zainwestował w nowoczesny system druku 3D z tworzyw. Na system ten składają się: Formlabs Fuse 1+ 30W / drukarka 3D do profesjonalnego druku 3D z tworzyw sztucznych Fuse Sift i Fuse Blast / 2 urządzenia do odzyskiwania proszku oraz czyszczenia wydruków Dzięki temu możliwe jest szybkie i ekonomiczne realizowanie indywidualnych zamówień – od prototypów, przez części zamienne, aż po gotowe produkty końcowe. Nowa maszyna pozwala drukować elementy z wytrzymałych materiałów, w tym poliamidów, poliuretanów oraz kompozytów, co otwiera szerokie możliwości dla branż takich jak medycyna, motoryzacja czy design. Cały proces – od projektu, przez druk, aż po postprocessing – odbywa się u nas na miejscu, co skraca czas realizacji i pozwala na błyskawiczne testowanie nowych rozwiązań. Klienci zyskują elastyczność, oszczędność czasu i pieniędzy oraz dostęp do wsparcia technicznego na najwyższym poziomie. Inwestycja w nową drukarkę 3D to nie tylko rozwój laboratorium Centrum Badawczo-Rozwojowego Hydropress, ale przede wszystkim realna wartość dodana dla naszych potencjalnych klientów, redefiniująca standardy prototypowania, produkcji niskoseryjnej oraz zaopatrzenia w części zamienne. Drukarka klasy Formlabs Fuse 1+ 30W to dostęp do przemysłowej technologii SLS, która do tej pory była zarezerwowana głównie dla dużych przedsiębiorstw produkcyjnych. Nowe możliwości dla klientów. Szybsze prototypowanie i produkcja niskoseryjna Fuse 1+ 30W pozwala na błyskawiczne przejście od fazy projektu do gotowego produktu. Dzięki możliwości drukowania wielu elementów jednocześnie (stacking w komorze roboczej), klienci mogą liczyć na znaczne skrócenie czasu realizacji zamówień oraz elastyczność w testowaniu i wdrażaniu nowych rozwiązań. Produkcja części końcowych o wysokiej wytrzymałości Drukarki obsługują szeroką gamę materiałów, w tym poliamidy (PA-12, PA-11), elastomery poliuretanowe (TPU) oraz materiały wzmacniane włóknem węglowym, co umożliwia wytwarzanie elementów o doskonałych właściwościach mechanicznych, odporności na temperaturę i ogniotrwałości. To otwiera nowe perspektywy dla branż takich jak automatyka przemysłowa, elektronika, AGD czy protetyka. Oszczędność i ekologia Technologia SLS umożliwia ponowne wykorzystanie do 80% proszku, co znacząco obniża koszty eksploatacji i zmniejsza ilość odpadów. Dodatkowo, drukarki nie wymagają specjalistycznych warunków lokalowych ani dodatkowej wentylacji, co ułatwia ich wdrożenie nawet w mniejszych firmach. Magazyn cyfrowy i produkcja na żądanie Zamiast gromadzić kosztowne zapasy części zamiennych, klienci mogą przechowywać modele cyfrowe i drukować elementy dokładnie wtedy, gdy są potrzebne. To minimalizuje ryzyko przestojów i pozwala na dynamiczne reagowanie na potrzeby rynku. Podsumowując, dzięki inwestycji w profesjonalną drukarkę 3D klasy Fuse 1+ 30W, laboratorium AMTH staje się centrum nowoczesnej produkcji addytywnej, oferując klientom: krótszy czas realizacji projektów większą elastyczność produkcyjną wyższą jakość i wytrzymałość wyrobów realne oszczędności oraz korzyści środowiskowe (mniejsze zużycie materiału - wydruk nie wymaga żadnych konstrukcji wsporczych) możliwość drukowania ruchomych części o skomplikowanej geometrii wewnętrznej wysoka jakość wydruków / gładka powierzchnia To krok milowy w kierunku cyfrowej transformacji produkcji i usług, który pozwali nam realizować nawet najbardziej zaawansowane projekty szybko, precyzyjnie i ekonomicznie.
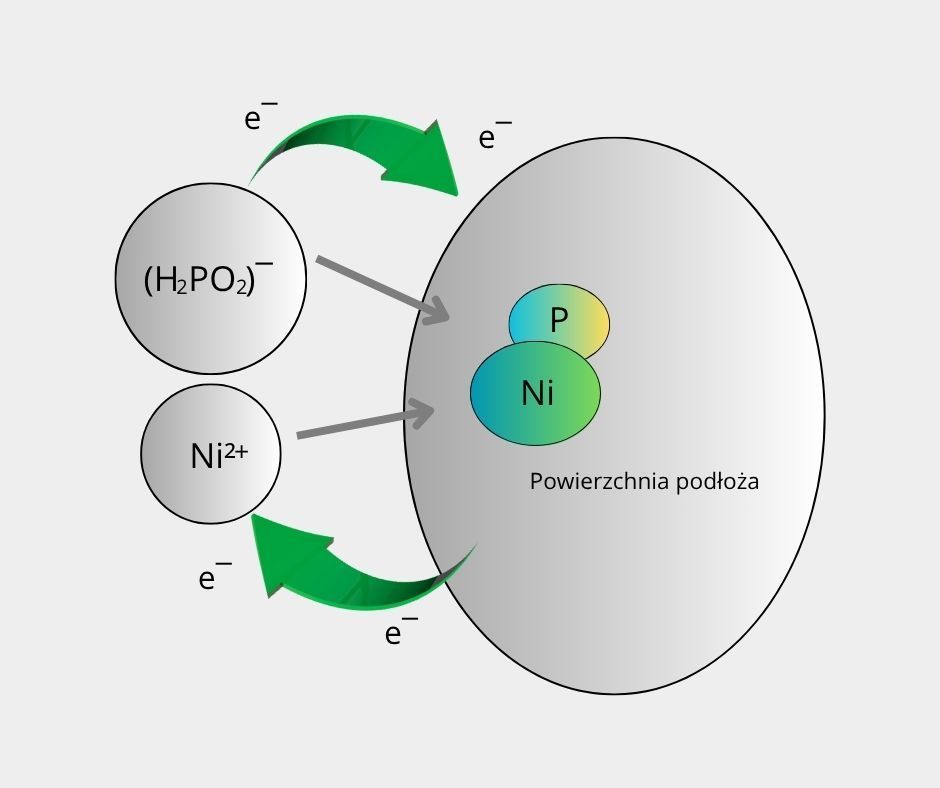
W wielu zastosowaniach przemysłowych odporność na korozję i zużycie to kluczowe wymagania stawiane częściom maszyn i narzędziom. Jedną z technologii, która zdobyła ogromną popularność w wielu branżach — od lotnictwa po produkcję form wtryskowych — są powłoki niklowe bezprądowe (ang. Electroless Nickel Plating, ENP). W odróżnieniu od tradycyjnego galwanicznego niklowania, tutaj nie potrzebujemy prądu. Proces zachodzi dzięki reakcjom chemicznym — i właśnie dzięki temu daje szereg unikalnych zalet. Na czym polega niklowanie bezprądowe? Powłoka niklowa bezprądowa powstaje w wyniku redukcji jonów niklu (Ni²⁺) na powierzchni obrabianego detalu przy udziale reduktora, najczęściej podfosforynu sodu (NaH₂PO₂). Reakcja przebiega w kąpieli chemicznej w odpowiedniej temperaturze (zwykle 80–95°C) i pH, bez konieczności przykładania napięcia. Podstawowa reakcja: Ni²⁺ + H₂PO₂⁻ + H₂O → Ni + H₂PO₃⁻ + H₂ W wyniku reakcji na powierzchni detalu powstaje jednorodna warstwa niklu z domieszką fosforu. Zalety powłok niklowych bezprądowych. ✅ Brak efektu krawędziowego — warstwa ma równą grubość nawet na skomplikowanych kształtach, w głębokich otworach, rowkach czy kanałach. ✅ Bardzo dobra odporność na korozję (szczególnie w wersjach wysokofosforowych). ✅ Wysoka twardość — nawet do 550 ± 50 HV bez obróbki cieplnej, a po starzeniu cieplnym nawet do 1000HV. ✅ Odporność na zużycie i tarcie — bardzo korzystna w formach wtryskowych, tłocznikach, zaworach, komponentach hydraulicznych. Rodzaje powłok w zależności od zawartości fosforu: Typ Zawartość P (%) Nisko fosforowe 2-5 Właściwości: Twarde, odporne na ścieranie, mniejsza odporność na korozję. Typ Zawartość P (%) Średnio fosforowe 6-9 Właściwości: Kompromis pomiędzy właściwościami mechanicznymi, a korozyjnymi. Typ Zawartość P (%) Wysoko fosforowe 10-13 Właściwości: Najlepsza odporność na korozję, nieco mniejsza twardość. Gdzie stosujemy powłoki ENP? ✅ przemysł lotniczy i kosmiczny ✅ przemysł naftowy i gazowy (rury, zawory, narzędzia wiertnicze) ✅ formy wtryskowe i tłoczniki ✅ hydraulika siłowa (tłoczyska, zawory, elementy precyzyjne) ✅ elektronika ✅ przemysł motoryzacyjny (wały, elementy zawieszenia, łożyska ślizgowe) Porównanie do powłok chromowanych W porównaniu do klasycznego chromowania galwanicznego, niklowanie bezprądowe (ENP) ma kilka istotnych przewag. Po pierwsze: pozwala uzyskać równomierną grubość powłoki nawet na skomplikowanych kształtach, gdzie chromowanie ma problem z równomiernością. Po drugie: powłoki ENP wykazują bardzo dobrą odporność na korozję, szczególnie w wersjach wysokofosforowych. Co równie ważne — ENP jest znacznie bezpieczniejsze ekologicznie. Klasyczne chromowanie wykorzystuje związki chromu sześciowartościowego (Cr⁶⁺), które są silnie toksyczne, rakotwórcze i podlegają ścisłym regulacjom środowiskowym (REACH, RoHS). Rysunek: „Inżynieria powierzchni” Marek Blicharski
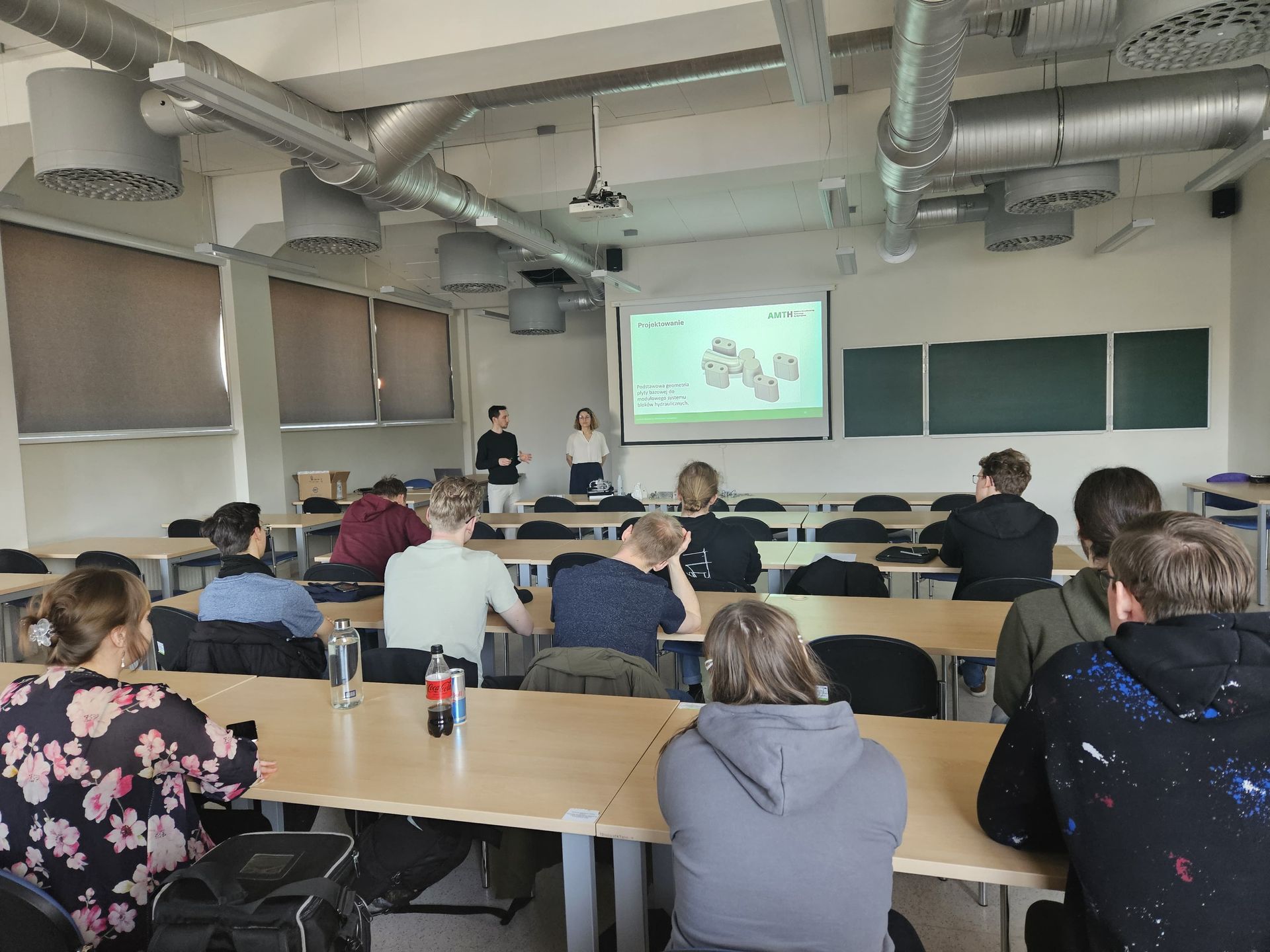
W jaki sposób można drukować z metalowego proszku? Czym jest projektowanie generatywne i gdzie jest wykorzystywane? Jakie są metody druku 3D i ich zalety? Studenci trzeciego roku na kierunkach Mechanika i Budowa Maszyn oraz Inżynieria Mechaniczno-Medyczna wzięli udział w warsztatach, na których mieli unikalną okazję uzyskania odpowiedzi na te pytania i wiele innych, związanych z innowacyjnymi technologiami druku 3D. Podczas tego spotkania nasi inżynierowie R&D podzielili się ze słuchaczami nie tylko swoją wiedzą, ale przede wszystkim swoim doświadczeniem z ostatnich kilkunastu miesięcy pracy z technologią DMLS (Direct Metal Laser Sintering) . Współpraca z Politechniką Gdańską Zajęcia odbywały się już po raz kolejny, w ramach współpracy z Politechniką Gdańską. Poza badawczo-naukowym wymiarem, współpraca od początku ma też charakter edukacyjny tj. ma na celu pogłębianie wiedzy o druku 3D u przyszłych inżynierów oraz prezentację tego zagadnienia od praktycznej strony. Najbardziej zaangażowani studenci mają szansę na staże i praktyki w Centrum Badawczo-Rozwojowym Hydropress, zlokalizowanym w Rumi. Wszystkim osobom, które wzięły udział w warsztatach, dziękujemy za inspirujące spotkanie. Zapraszamy na kolejne.
Targi "Przemysłowa Wiosna" w Kielcach to jedno z najważniejszych wydarzeń w świecie nowoczesnych technologii produkcyjnych. Szczególne miejsce wśród prezentowanych innowacji zajmuje druk 3D, który z roku na rok zdobywa coraz większe zainteresowanie zarówno wśród profesjonalistów, jak i pasjonatów. Dni Druku 3D – kilka dni inspiracji Jednym z najbardziej wyczekiwanych segmentów targów są Dni Druku 3D, które co roku przyciągają czołowych producentów drukarek z Polski i zza granicy oraz firmy, zajmujące się drukiem 3D, skanowaniem 3D oraz szybkim prototypowaniem. To wydarzenie nie tylko potwierdza swoją ugruntowaną pozycję na rynku, ale także dynamicznie się rozwija, z roku na rok przyciągając coraz większą liczbę wystawców i zwiedzających. Dla inżynierów R&D w AMTH targi były wyjątkową inspiracją oraz doskonałą okazją do rozmów kuluarowych z zaprzyjaźnionymi firmami oraz lidearmi w branży. Rozwój i przyszłość druku 3D Technologie druku 3D, skanowania 3D i szybkiego prototypowania to kluczowe elementy rozwoju nowoczesnych przedsiębiorstw. Firmy myślące o przyszłości inwestują w innowacyjne rozwiązania, które pozwalają na zwiększenie efektywności produkcji i redukcję kosztów. Przemysłowa Wiosna w Kielcach to miejsce, gdzie przyszłość produkcji spotyka się z teraźniejszością, a innowacje w druku 3D odgrywają kluczową rolę w kształtowaniu nowoczesnego przemysłu. Zapraszamy na relację.
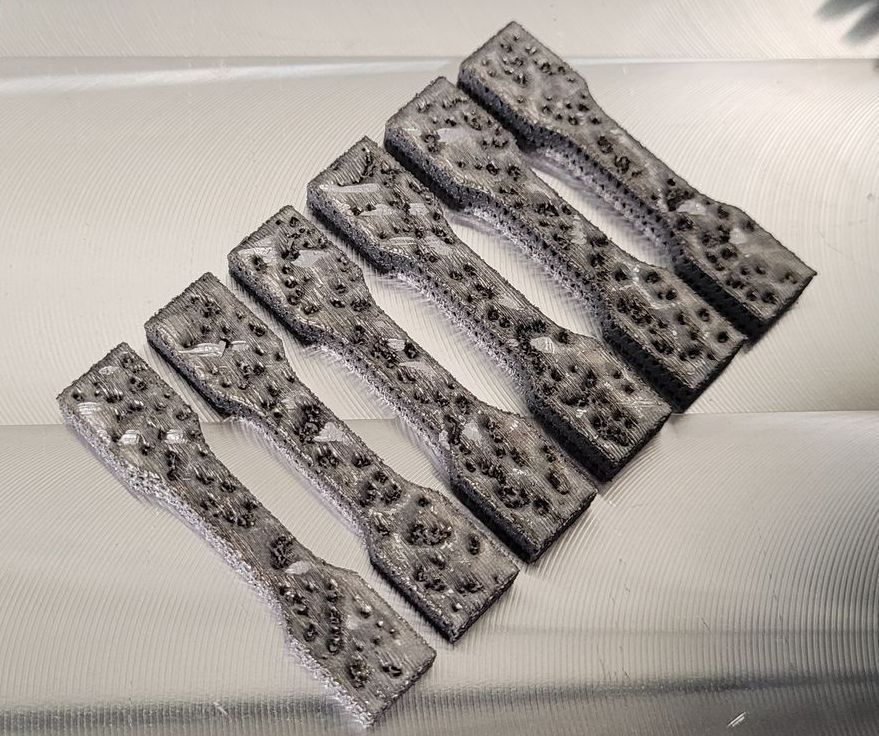
Z przyjemnością informujemy, że wyniki badań prowadzonych przez nas we współpracy z Wydziałem Mechatroniki i Budowy Maszyn Politechniki Świętokrzyskiej zostały opublikowane w prestiżowym czasopiśmie naukowym "Materials MDPI". Publikacja prezentuje ocenę właściwości wytrzymałościowych i struktury powierzchni modeli cienkościennych, wykonanych z proszku aluminiowego AlSi10Mg w technologii druku 3D typu Powder Bed Fusion (PBF). Celem badań było określenie technologicznych ograniczeń produkcji elementów cienkościennych oraz ocena wpływu grubości modeli oraz kierunku drukowania na właściwości mechaniczne i jakość powierzchni. Wyniki tych analiz mają szczególne znaczenie praktyczne. Pozwalają na optymalizację, już na etapie projektowania. Efekty prac można z powodzeniem wykorzystać m.in. na potrzeby wytwarzania komponentów w hydraulice siłowej, prowadząc do zmniejszenia masy oraz zwiększenia efektywności przepływu płynów w układach hydraulicznych. Zainteresowanych wynikami badań zapraszamy do artykułu źródłowego: Evaluation of Selected Quality Characteristics of Thin-Walled Models Manufactured Using Powder Bed Fusion Technology Autorami artykułu są: dr hab. inż. Tomasz Kozior prof. PŚk. Politechnika Świętokrzyska w Kielcach dr hab. inż. Jerzy Bochnia prof. PŚk. Politechnika Świętokrzyska w Kielcach Alicja Jurago Inżynier R&D Hydropress Michał Adamczyk Dyrektor ds. technicznych Hydropress Piotr Jędrzejewski Inżynier R&D Hydropress Dziękujemy wszystkim współautorom za owocną współpracę.
Firma Czinger Vehicles, założona przez Kevina i Lukasa Czingerów, opracowała innowacyjny proces produkcyjny nowoczesnych pojazdów, który zrewolucjonizuje tradycyjne podejście do metod produkcji w branży motoryzacyjnej. Czinger Vehicles przy produkcji hipersamochodu szeroko wykorzystuje technologie druku 3D i generatywne projektowanie, wspomagane sztuczną inteligencją. Pozwala to na wytwarzanie ultralekkich i wytrzymałych komponentów oraz na zminimalizowanie liczby części i ich połączeń, w porównaniu z tradycyjnym modelem. Jednym z najistotniejszych dla projektu rozwiązań okazały się elementy konstrukcyjne Czingera 21C – wydrukowane w technologii 3D aluminiowe złącza. Ich zastosowanie przełożyło się nie tylko na znaczące zredukowanie masy samochodu, ale także zwiększyło jego sztywność i bezpieczeństwo. Dzięki takiej konstrukcji Czinger 21C osiągnął imponujące parametry wydajności i efektywności, wyznaczając nowe standardy w branży motoryzacyjnej. Wykorzystanie druku 3D i generatywnego projektowania w procesie tworzenia tak zaawansowanego pojazdu jak Czinger 21C okazało się kluczowe z kilku powodów: • pozwoliło zoptymalizować czas od pomysłu do wdrożenia przez szybkie prototypowanie • uprościło wprowadzanie na bieżąco niezbędnych modyfikacji w wytwarzanych komponentach pojazdu • zredukowało ilość odpadów produkcyjnych i zużycie materiałów, co przełożyło się na finalne koszty realizacji, z uwzględnieniem najwyższych standardów zrównoważonego rozwoju. 21C napędzany jest 2,9-litrowym, podwójnie turbodoładowanym silnikiem V8 o mocy 950 koni mechanicznych. Czinger łączy go z 800-woltowym układem elektrycznym, 2,8-kilowatogodzinnym akumulatorem, silnikiem elektrycznym na przedniej osi i dwoma silnikami na tylnej osi. Waga pojazdu 1315 kg Model 21C posiada homologację do użytku drogowego w USA, spełniając wszystkie normy testów zderzeniowych i emisji spalin. Podsumowując: Czinger 21C to nie tylko przełomowy hipersamochód pod względem osiągów, zarejestrowanych podczas testów, ale także pionier w zastosowaniu druku 3D w motoryzacji. W pełni odsłania potencjał tej technologii w tworzeniu bardziej zaawansowanych, lekkich i ekologicznych pojazdów.
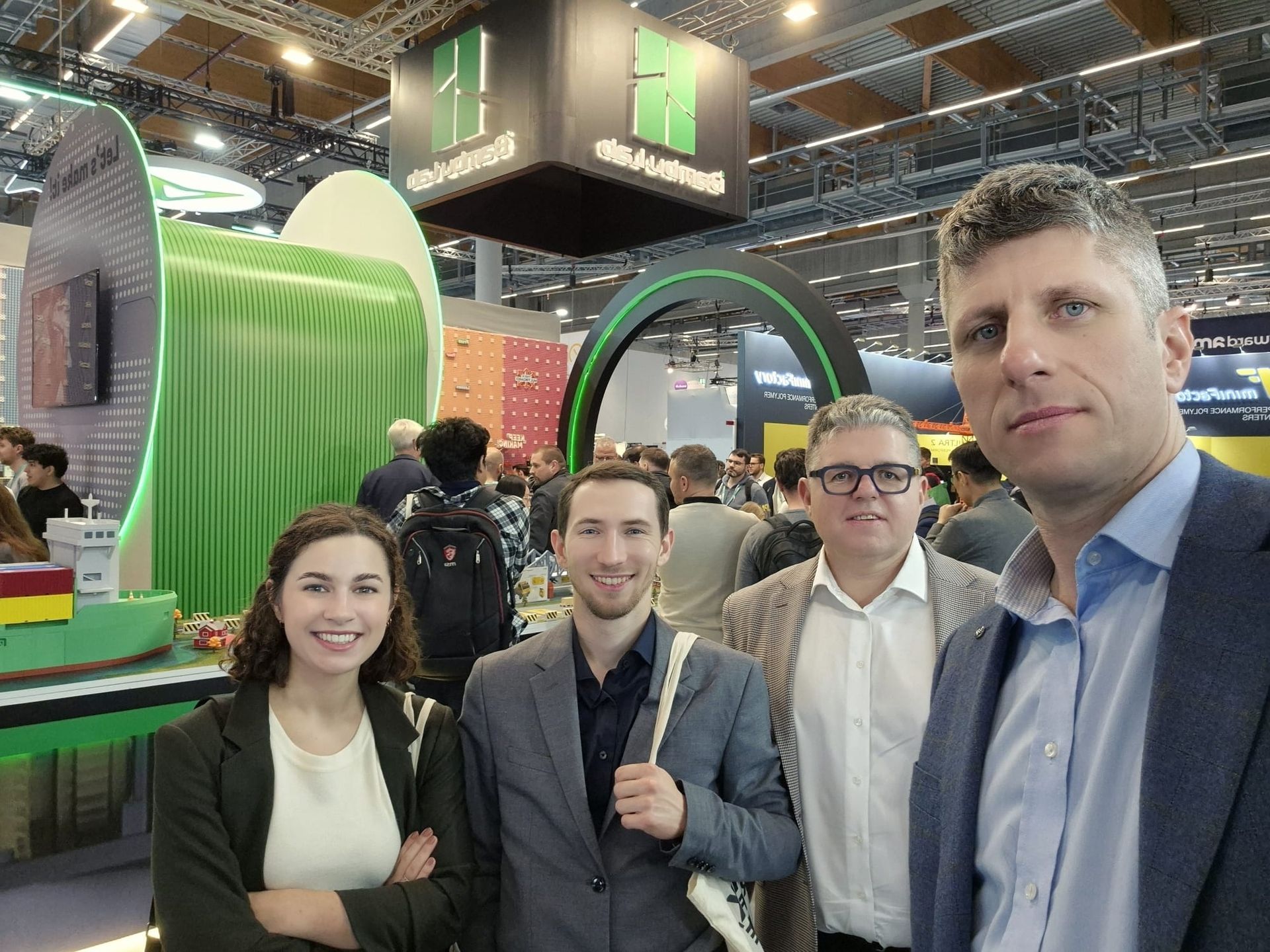
Druk 3D bezpowrotnie zmienił łańcuch procesów od idei produktu do jego produkcji. Dużo się dzieje i praktycznie każdy dzień przynosi innowacyjne rozwiązania, we wszystkich branżach. Doskonale było to widoczne na Formnext, największych międzynarodowych targach technologii addytywnych, które odbyły się we Frankfurcie. Ponad 400 międzynarodowych wystawców i tysiące odwiedzających z całego świata. To obowiązkowy punkt na targowej mapie każdego, kto poważnie myśli o rozwoju swojego biznesu. Z każdym rokiem widać coraz więcej zastosowań druku 3D i dynamiczny wzrost skali produkcji, zarówno patrząc na rozmiary drukowanych elementów jak i coraz większe ilości produkowane seryjnie. W druku z metalu prym wiedzie przemysł kosmiczny, który perfekcyjnie wykorzystuje zalety druku do tworzenia coraz większych i bardziej złożonych komór spalania silników rakietowych. One szczególnie przyciągały uwagę wszystkich zwiedzających. Inne popularne rozwiązania to chłodnice, części do motoryzacji i sportu, narzędzia i coraz większe elementy do maszyn obróbczych. Nie zabrakło też produktów z branży hydrauliki siłowej, co ze względów oczywistych bardzo nas interesowało. Podsumowując- to był dla nas dobrze spędzony czas.
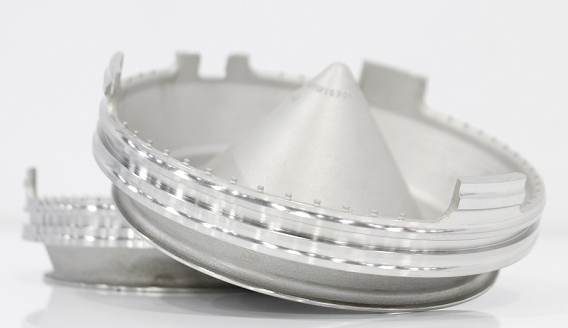
Pokrywa skrzyni korbowej silnika GE F110. Skrzynia korbowa jest częścią układu smarowania olejowego, a jej pokrywa jest kluczową częścią silnika. Siły Powietrzne USA wymagają jedynie trzech do pięciu wymian miski olejowej F100 rocznie. Czas oczekiwania na otrzymanie tej części w normalnych łańcuchach dostaw często zajmuje ponad 18 miesięcy. Centra logistyki lotniczej mogłyby pokonać te wyzwania dzięki własnym możliwościom wytwarzania przyrostowego.

BMW wykorzystuje technologię druku 3D już od 1991 roku, zaczynając od produkcji części i form na odlewy. W 2015 roku w Centrum Badań i Innowacji FIZ w Monachium powstało 100 000 elementów wyłącznie dla potrzeb wewnętrznych. Drukowane części odchodzą już od samych prototypów, czy elementów wspomagających tradycyjne procesy odlewnicze, a coraz częściej druk 3D wykorzystywany jest do końcowych produktów - jednym z takich przykładów jest wytworzony w ilości już kilkuset sztuk wirnik pompy wodnej. Wirnik pompy wodnej w pojeździe odpowiada za przetłaczanie cieczy w systemie chłodzącym, co umożliwia pracę silnika w optymalnej temperaturze. Ten precyzyjny element, który przez swe techniczne życie poddawany jest niesłychanym obciążeniom odnajduje swoje zastosowanie w wyścigach Deutsche Tourenwagen Masters. Względem tradycyjnie wykonanego odpowiednika jest tańszy i prostszy w wykonaniu.
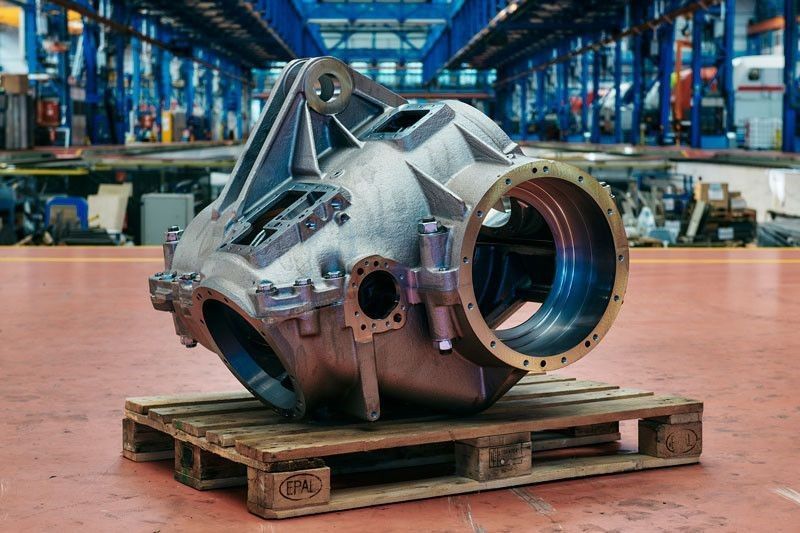
Ostatnia wydrukowana w 3D część to obudowa przekładni lokomotyw manewrowych: o imponujących wymiarach prawie jednego metra sześciennego objętości i wadze 570 kg jest to największa i najcięższa wydrukowana w 3D część, jaką firma kiedykolwiek wyprodukowała przy użyciu technologii wytwarzania addytywnego. Konwencjonalne zaopatrzenie w części zamienne wiąże się z długim czasem dostawy wynoszącym średnio dziesięć miesięcy – dzięki drukowanej formie piaskowej stworzonej metodą strumieniowego odlewania spoiwem, proces produkcji można było znacznie przyspieszyć, dzięki czemu komponent może być teraz dostępny w ciągu dwóch miesięcy. Inna zaleta pośredniego drukowania 3D z szybkim odlewaniem: dzięki tej procedurze komponent pozostaje w swoim pierwotnym trybie produkcji, ponieważ drukowana jest tylko forma dla odlewanego komponentu.
Bądź na bieżąco z nowościami!
Jesteśmy podekscytowani, mogąc podzielić się z Tobą najnowszymi wiadomościami ze świata druku 3D.
Zapisz się do naszego newslettera, żeby być jednym z pierwszych, którzy dowiadują się o postępach naszego projektu i efektach badań.
Zostaw swój e-mail, aby:
- Otrzymywać regularne aktualizacje o kluczowych etapach projektu Hydropress.
- Być informowanym o otwarciu zamówień komercyjnych.
- Mieć dostęp do ekskluzywnych treści i promocji.